Mechanical Stress Sensor
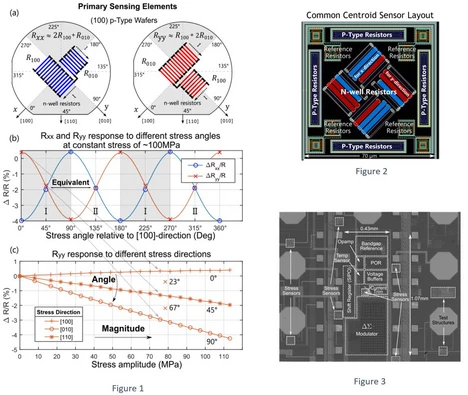
Figure 2: Layout of the sensing elements [12].
Figure 3: Micrograph of the test chip with seven distributed stress sensors [12].
In emerging application areas such as health monitoring, industrial automation and advanced robotics, there is an increasing need for low-cost, highly integrated yet accurate mechanical stress measurement systems. Currently the most commonly used mechanical stress sensors are capacitor based. While these sensors are widely used in consumer electronics, they are still limited in terms of information they can extract from the stimulus.
With the expansion in the field of robotics in the last few decades, there has been an unprecedented growth in the research of stress sensing mechanisms. One of the most popular research topics focuses on the use of piezoresistive devices to create tactile sensors for artificial skin. While the piezo-resistive property of semiconductors has been a topic of research for many years now [1-4], there are constant improvements made by combining them with polymer composites to create more robust, flexible sensors. There are also many recent examples in literature [5], [6] where materials such as graphene and CNT are used to enhance the sensitivity and performance of the stress sensors. These papers, even though show promising results, require non-traditional fabrication steps and hence cannot be used in a large scale.
Use of silicon-based sensors, therefore, offer a great advantage over composite materials. The piezo-resistive behavior of silicon is a function of its orientation and hence the stress sensitivity changes with the direction of the applied stress. This inherent directional sensitivity of silicon makes it extremely easy to differentiate between orthogonal stress components, and hence, is superior to capacitive sensing. Additionally, these sensors can be manufactured while remaining within the bounds of current available fabrication technologies, making them ideal for commercial applications.
Leveraging the well-known benefits of CMOS technology, namely the large-scale production of cost-efficient and feature-rich solutions, recent publications [7–11] also provide examples of state-of-the-art strain gauges that can measure weight, deformation, and structural details of goods and equipment. Furthermore, these devices have already found use in orthodontic brackets [10], [11] and can even mimic the properties of human skin [7].
Adding to the literature, we expand upon our related work presented in [12], which offers a fully integrated CMOS stress sensor that simultaneously exhibits wide dynamic range, low-power consumption, and is robust over-temperature and process variation. Moreover, the sensor system is designed to measure both the magnitude and the angle of mechanical stress. By combining these two features, we are targeting two main applications: On-chip sensors for mechanical stress evaluation and stress sensors for predictive maintenance (Industry 4.0) and other Internet of Things (IoT) use cases (such as electronic skin).
On-chip sensors enable the investigation of different types of IC packages in terms of mechanical stress under different environmental conditions. Distributed sensor elements in ICs also provide information on local absolute stress values as well as stress gradients between the sensor elements.
By keeping the trade-off between area, power and cost in mind, we can alter the performance of the sensor to meet various application-specific requirements. Extending the same principle shown in [12], we can further increase the stress sensitivity and measure stress values as low as tens of kilo-Pascals. At such low values of stress, the 1/f noise, especially while working in low frequency applications, becomes the biggest challenge. Considering that most common noise reduction techniques either come at the cost of high power or area, finding an optimum solution becomes critical for applications where multiple such chips need to be used in a distributed network. Therefore, the current work at the chair aims to find smart solutions to solve this issue.
Figure 4 shows the top-level block diagram for the entire chip. It can be seen that all components of our design, i.e., the piezoresistive sensors, amplifier, ADC, and the digital and I2C logic blocks, are all integrated within the same chip. All chips in the final tactile sensing array will be connected using
only an I2C bus. This makes the interface between the proposed tactile skin and the MCU purely digital and more robust against noise. The complete tactile skin patch targets a 60 Hz refresh rate (16.6 ms), similar to any standard touch-based application. As mentioned in the previous section, the data communication happens via a 400 kHz I2C clock. The MCU initiates the communication, and all the chips in the array act as targets that transmit data when polled by the MCU.
Reference
M. Meyers and K. Chawla, Mechanical Behavior of Materials. Cambridge, U.K.: Cambridge Univ. Press, 2009, pp. 86–92.
Y. Kanda, “Piezoresistance effect of silicon,” Sens. Actuators A, Phys., vol. 28, no. 2, pp. 83–91, Jul. 1991.
Y. Kanda, “A graphical representation of the piezoresistance coefficients in silicon,” IEEE Trans. Electron Devices, vol. ED-29, no. 1, pp. 64–70, Jan. 1982.
F. Fruett and G. C. M. Meijer, The Piezojunction Effect in Silicon Integrated Circuits and Sensors. Norwell, MA, USA: Kluwer, 2003, pp. 42–44.
Gong, Tianxun, et al. "Highly responsive flexible strain sensor using polystyrene nanoparticle doped reduced graphene oxide for human health monitoring." Carbon 140 (2018): 286-295.
Seong, M.; Hwang, I.; Lee, J.; Jeong, H.E. A Pressure-Insensitive Self-Attachable Flexible Strain Sensor with Bioinspired Adhesive and Active CNT Layers. Sensors 2020, 20, 6965.
Y. Mahsereci, S. Sailer, H. Richter, and J. N. Burghartz, “An ultrathin flexible CMOS stress sensor demonstrated on an adaptive robotic gripper,” IEEE J. Solid-State Circuits, vol. 51, no. 1, pp. 273–280, Jan. 2016.
J. L. Ramirez and F. Fruett, “Multi-terminal piezoMOSFET sensor for stress measurements in silicon,” in Proc. 31st Symp. Integr. Circuits Syst.Design (SBCCI), Aug. 2018, pp. 1–6.
J. L. Ramirez and F. Fruett, “Integrated octagonal mechanical stress sensor with temperature compensation,” IEEE Sensors J., vol. 18, no. 14, pp. 5707–5714, Jul. 2018.
M. Kuhl et al., “A telemetric stress-mapping CMOS chip with 24 FETbased stress sensors for smart orthodontic brackets,” in Proc. IEEE Int. Solid-State Circuits Conf., Feb. 2011, pp. 108–110.
M. Kuhl et al, “A wireless stress mapping system for orthodontic brackets using CMOS integrated sensors,” IEEE J. Solid-State Circuits, vol. 48, no. 9, pp. 2191–2202, Sep. 2013.
U. Nurmetov et al., "A CMOS Temperature Stabilized 2-D Mechanical Stress Sensor With 11-bit Resolution," in IEEE Journal of Solid-State Circuits, vol. 55, no. 4, pp. 846-855, April 2020.
V. Verma, A. N. I. Torrent, D. Petrić, V. Haberhauer and R. Brederlow, "Silicon-Based Piezoresistive Stress Sensor Arrays for Use in Flexible Tactile Skin," in IEEE Transactions on Biomedical Circuits and Systems, vol. 18, no. 4, pp. 834-848, Aug. 2024.